Heritage, style, performance and emissions free – the AC Cobra Series 4–electric is an AC Superblower updated for the new world, and the latest model in the redux of an iconic marque.
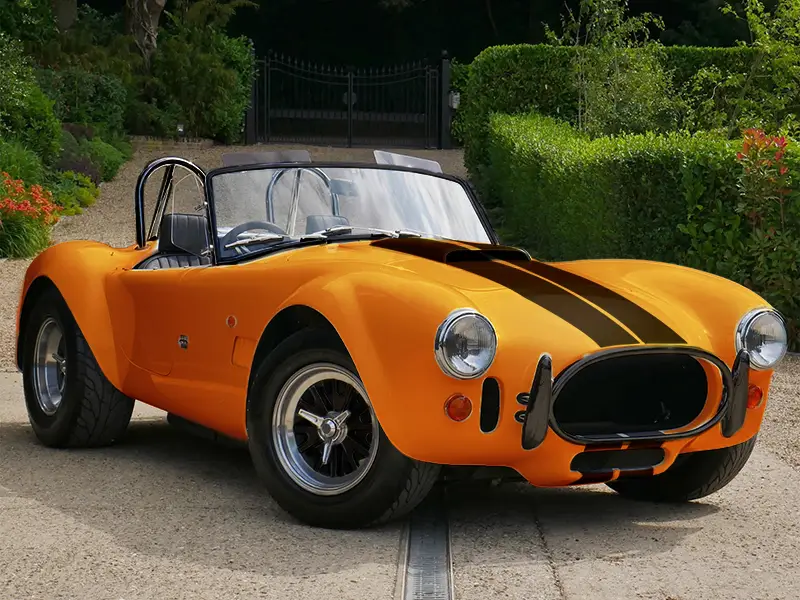
Heritage, style, performance and emissions free – the AC Cobra Series 4–electric is an AC Superblower updated for the new world, and the latest model in the redux of an iconic marque.
Leading electrified powertrain engineering consultancy, Drive System Design (DSD), has announced a strategic expansion of its test facilities, adding two further test cells for high-performance hybrid axles and e-machines. The move reflects a growing demand for outsourced test capacity suitable for electrified powertrains, as the industry prioritises its development in response to global emissions concerns.
The first of the new facilities can deliver input torque up to 2,500Nm at 2,100rpm, 525kW at 7,000rpm, and 350kW 1,100V of battery emulation, with the second for e-machines up to 350kW and 25,000rpm. The new cells complement existing DSD facilities, which include a 450kW highly transient ETPS machine (Engine Torque Pulse Simulator) and three battery emulators.
“The recent Covid-19 pandemic has put an ever-bigger spotlight on our environment and recent government announcements on ICE restrictions is resulting in a faster shift to electrified vehicles than first anticipated,” explains David Kelly, Director, Drive System Design. “There is a significant increase in demand globally, not only for design and development work but also for outsourced testing. The additional facilities will extend our ability to provide this for a wide range of hybrid and electric powertrains.”
According to Kelly, even the largest, established vehicle manufacturers are struggling to accommodate the upsurge in test requirements using solely in-house facilities, and the situation is likely to become even more acute in future. “We are in the middle of a sea change in the industry, as the major players allocate more of their manufacturing to electrified vehicles,” he says. “Companies like DSD can provide vital additional resource to help satisfy short-term peaks in testing demand as this change in policy takes effect.”
DSD is continually developing its automation capabilities within the facility to help speed up testing. This has proven particularly effective in the case of hot and cold environment testing. According to Kelly, tests that previously took six weeks to complete can be finished in half the time with suitably configured automatic control.
DSD intends to have the new test cells operational in December this year.
www.drivesystemdesign.com
• SYNETIQ to expand Doncaster site by 25 acres
• New plant to handle more vehicles, more efficiently than ever before
• Planning permission granted for the expansion into existing brownfield land
• Continues company’s investment into the South Yorkshire region
• Part of SYNETIQ’s strategy to operate from fewer but larger sites
• UK-based D2H introduces aerodynamic simulation to pre-season control testing regime
• VCAT test days now incorporate use of bespoke active ride-height system designed and developed by D2H
• Data sharing ensures all non-homologated teams can benefit from VCAT test results
• Saietta Group wins significant Advanced Propulsion Centre grant
• Funding to fast-track production of company’s proprietary EV motor technology
• Allows production of 150,000 units per annum and creates 150-250 new jobs
• MAHLE invests around EUR 3 million in new test bench in Stuttgart
• Testing and development of e-axles and e-drive units for electric and hybrid vehicles
• Successful completion of first customer project
Watch the build of Team BRIT’s BMW M240i race car
The long and thrilling story of one of the most iconic British sports cars is about to open a new and remarkable chapter.
One of the UK’s best-known companies, British Gas’ heritage stretches back over 200 years. Its iconic bright blue vans are a regular sight on the road, carrying thousands of Engineers between homes and businesses.
At around 11,400 vehicles, the British Gas fleet is one of the largest in the country; managing something that size comes with significant responsibilities. The business is always open to exploring new, innovative ways of working, considering everything from environmental performance to the practicalities of vehicle downtime and cost reduction.
“We’re constantly considering new initiatives to keep our engineer’s mobile whilst doing right by our customers, employees and the environment,” explains Steve Winter, Head of Fleet at British Gas, In March 2020, the business was named as Fleet of the Year at the Fleet News’ Awards, for its range of initiatives concerning vehicle downtime, driver welfare and environmental performance.
As a trusted partner SYNETIQ, the UK’s largest salvage and vehicle recycling company, plays a vital role in keeping the wheels turning. British Gas is in partnership with SYNETIQ MyGreenFleet, which delivers intelligent solutions and the compliant handling of British Gas salvage vehicles. No salvage vehicles are resold, with the shells crushed and recycled on site, ensuring they can never return to the road.
Some vehicles still contain perfectly good, non-safety-related parts – known as green parts – and these are sold back to British Gas repair partners (Hitachi and SOPP+SOPP) for re-use on its own vehicles. This simple, yet incredibly effective, process has helped British Gas save millions of pounds since it began in 2012.
“What surprises me is the number of fleets which aren’t considering the use of green parts,” says Steve. “The cost savings and environmental benefits are clearly visible in the data provided by SYNETIQ, and we’re happy with the service provided.”
SYNETIQ green parts are OEM, non-safety critical, quality-controlled parts, such as doors, bumpers, and lights, and are perfect for reuse on damaged repairable British Gas vehicles. Parts are often already painted and stickered to match and are delivered to British Gas accident/fleet management partners, using SYNETIQ MyGreenFleet inhouse logistics, within 48 hours. This means Engineers can get back on the road more quickly, and unnecessary manufacturing of new parts is reduced.
Since 2012, SYNETIQ MyGreenFleet have supplied over 1200 doors alone, for use on British Gas vehicles – saving more than 120,000kg of CO2 against comparable new doors. Over 6500 non-safety related green parts have been supplied in total, generating a truly significant saving.
Green parts are up to 70% cheaper when compared with new, OEM parts, and act as a like for like replacement. Accurate data is available to British Gas within MyGreenFleet, providing insight on cost savings, units, and performance against agreed service level agreements – such as delivery time. Use of green parts often reduces vehicle downtime, meaning Engineers can get back on the road more quickly.
Jason Cross, Client Relationship Director at SYNETIQ, says the business is proud to be trusted by British Gas. “We like saying yes,” says Jason. “We pride ourselves on removing the barriers or problems that crop up when operating such a vast fleet.”
SYNETIQ also provides ‘waste and destock’ services, where a SYNETIQ employee can empty vans of equipment and personal belongings and securely return them, disposing of any waste.
Technical equipment used by Engineers can also be transferred from one vehicle to another in the event of it switching drivers. Ladders and scales are stored securely on SYNETIQ sites, and either returned to British Gas or transferred to another vehicle. This protects valuable equipment from theft and further reduces ‘vehicle of road’ (VOR) time.
“We’re very proud to be trusted by British Gas – it means a lot to our business,” says Jason. “I’m pleased to share that Steve recently awarded us a score of ‘10’ in our recent client satisfaction survey. We’re looking forward to working with them to provide more intelligent solutions for the future.”
Cookie | Duration | Description |
---|---|---|
__hssrc | session | This cookie is set by Hubspot whenever it changes the session cookie. The __hssrc cookie set to 1 indicates that the user has restarted the browser, and if the cookie does not exist, it is assumed to be a new session. |
cookielawinfo-checkbox-advertisement | 1 year | Set by the GDPR Cookie Consent plugin, this cookie is used to record the user consent for the cookies in the "Advertisement" category . |
cookielawinfo-checkbox-analytics | 1 year | Set by the GDPR Cookie Consent plugin, this cookie is used to record the user consent for the cookies in the "Analytics" category . |
cookielawinfo-checkbox-functional | 1 year | The cookie is set by the GDPR Cookie Consent plugin to record the user consent for the cookies in the category "Functional". |
cookielawinfo-checkbox-necessary | 1 year | Set by the GDPR Cookie Consent plugin, this cookie is used to record the user consent for the cookies in the "Necessary" category . |
cookielawinfo-checkbox-others | 1 year | Set by the GDPR Cookie Consent plugin, this cookie is used to store the user consent for cookies in the category "Others". |
cookielawinfo-checkbox-performance | 1 year | Set by the GDPR Cookie Consent plugin, this cookie is used to store the user consent for cookies in the category "Performance". |
CookieLawInfoConsent | 1 year | Records the default button state of the corresponding category & the status of CCPA. It works only in coordination with the primary cookie. |
Cookie | Duration | Description |
---|---|---|
__cf_bm | 30 minutes | This cookie, set by Cloudflare, is used to support Cloudflare Bot Management. |
__hssc | 30 minutes | HubSpot sets this cookie to keep track of sessions and to determine if HubSpot should increment the session number and timestamps in the __hstc cookie. |
bcookie | 2 years | LinkedIn sets this cookie from LinkedIn share buttons and ad tags to recognize browser ID. |
bscookie | 2 years | LinkedIn sets this cookie to store performed actions on the website. |
lang | session | LinkedIn sets this cookie to remember a user's language setting. |
lidc | 1 day | LinkedIn sets the lidc cookie to facilitate data center selection. |
UserMatchHistory | 1 month | LinkedIn sets this cookie for LinkedIn Ads ID syncing. |
Cookie | Duration | Description |
---|---|---|
__hstc | 5 months 27 days | This is the main cookie set by Hubspot, for tracking visitors. It contains the domain, initial timestamp (first visit), last timestamp (last visit), current timestamp (this visit), and session number (increments for each subsequent session). |
_ga | 2 years | The _ga cookie, installed by Google Analytics, calculates visitor, session and campaign data and also keeps track of site usage for the site's analytics report. The cookie stores information anonymously and assigns a randomly generated number to recognize unique visitors. |
_gat_gtag_UA_170839631_1 | 1 minute | Set by Google to distinguish users. |
_gid | 1 day | Installed by Google Analytics, _gid cookie stores information on how visitors use a website, while also creating an analytics report of the website's performance. Some of the data that are collected include the number of visitors, their source, and the pages they visit anonymously. |
CONSENT | 2 years | YouTube sets this cookie via embedded youtube-videos and registers anonymous statistical data. |
hubspotutk | 5 months 27 days | HubSpot sets this cookie to keep track of the visitors to the website. This cookie is passed to HubSpot on form submission and used when deduplicating contacts. |
Cookie | Duration | Description |
---|---|---|
VISITOR_INFO1_LIVE | 5 months 27 days | A cookie set by YouTube to measure bandwidth that determines whether the user gets the new or old player interface. |
YSC | session | YSC cookie is set by Youtube and is used to track the views of embedded videos on Youtube pages. |
yt-remote-connected-devices | never | YouTube sets this cookie to store the video preferences of the user using embedded YouTube video. |
yt-remote-device-id | never | YouTube sets this cookie to store the video preferences of the user using embedded YouTube video. |
Cookie | Duration | Description |
---|---|---|
AnalyticsSyncHistory | 1 month | No description |